記事ランキング
-
【第1位】
コスト削減・安定品質を実現する 車載... -
【第2位】
プレス加工によるコスト改善をご提案。... -
【第3位】
プレス金型を使った自動組立装置で組立... -
【第4位】
試作用母型のご案内
微細プレス加工への挑戦|マイクロピッチコネクタ、銅箔電子基板インプラント加工、銅箔などの複合素材に微細穴の連続加工
鈴木はこれまでにコネクタコンタクトを代表する数多くの微細なプレス加工部品を製造してきました。昨今のテクノロジーの進化とともに、さらに微細で高精度な部品供給が求められています。
次世代ニーズに対応するために、金型の精度をより高く、緻密で高品質な部品加工に日々挑戦しています。鈴木の技術力でお客様の難題を一緒に解決していきます。
微細プレス加工への挑戦 その1
通常の電子コネクタの1/10サイズ
正確で均一な20μmのスリット打ち抜きによるマイクロピッチコネクタ
微小幅20μmのスリット打ち抜き加工と、リード先端の曲げ加工をマイクロピッチコネクタでのプレス加工で挑戦した事例です。
正確で均等な打ち抜き加工により、断面をカットしても不要な接触や変形が発生しません。また、リード先端の曲げ加工もスリットを入れてから行なっていますが、正確な打ち抜きにより変形せず素直な曲げを実現しています。
微細プレス加工のポイント
スリット幅20μm、リード幅80μmの順送プレス加工(送りピッチ0.1mm)
正確な抜き打ちで、リード先端を曲げても変形しない
超微細金型のため工具を独自開発
開発した工具
- 先端径20μm以下の砥石
- 長さ0.15mm、幅0.02mmのパンチ
- 親指サイズの精密バイス
- 金型と材料一体型の送り装置(送り精度±01μm、移動範囲150mm)
微細プレス加工への挑戦 その2
銅箔電子基板の表裏導通を図りインプラント加工の生産性を向上
「ビアホール加工」「金属充填」「カシメ」を1工程で実現
銅箔電子基板の表裏導通を図るために、微細穴に金属充填を行うインプラント加工。
高精度なプレスで「ビアホール加工」「金属充填」「かしめ」を1工程で行うことで生産性を向上しています。
めっき加工による穴あけと違い、溶剤を使わないので環境にもやさしい技法です。
微細プレス加工のポイント
パンチング金型技術によるスルーホールと金属充填の同時加工
- ビアホール加工 →インプラント材充填 →カシメ
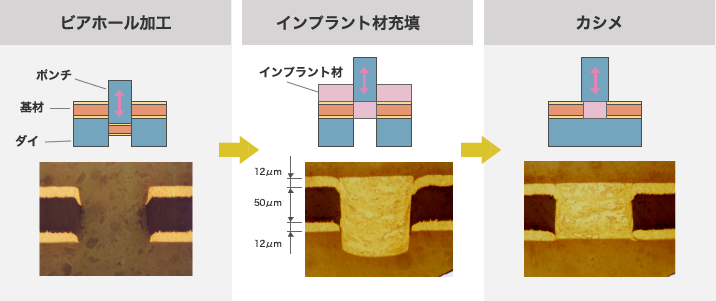
【加工条件】
・基板 銅箔12μm/ポリイミド50μm/銅箔12μm
・インプラント材 無酸素銅(C1020)
・インプラント直径 φ100μm
バンプ形成が簡単
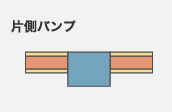
多層構造のインプラント材を利用可能
その他応用例 2メタルTABの表裏導通、多層基板の層間導通、放熱用 など
微細プレス加工への挑戦 その3
ポリイミドや銅箔などの複合素材に微細穴の連続加工
量産性を見据え、従来工法やエッチングできない複合材料をプレスに転換
穴あけ加工の方法として、エッチングやレーザー、放電、ドリルなど様々な選択肢がありますが、量産時には、コストを抑えられるプレス加工を選びたいという相談は多くあります。
鈴木ではお客様と一緒に課題を解決するスタンスで、プレス加工を前提としてコスト面を考慮した部品形状をご提案をいたします。
微細プレス加工のポイント
高精度な穴あけ部品を低コストで安定供給
エッチングできない複合材料の加工をプレス化
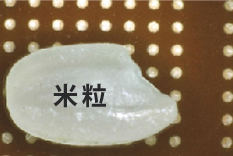
Ø280μm
ピッチ650μm
・素材:ポリイミド+接着剤+カバーテープ
・無給油加工
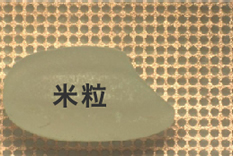
Ø250μm
ピッチ300μm
・素材:銅箔+α
・給油加工
微細プレス加工への挑戦 その4
外形Ø200μm、長さ800μmの圧着端子の順送金型プレス加工
プレス金型における「抜き」「曲げ」「絞り」「潰し」の各要素技術を必要とする従来の端子形状のまま、どこまで微細化に対応できるかチャレンジした事例です。
大きさ比較
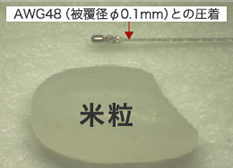
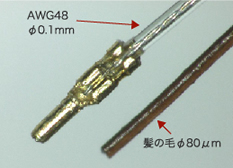
丸加工による貫通穴
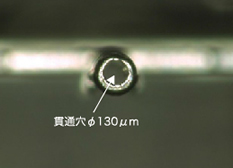
ソケットとプラグの形状
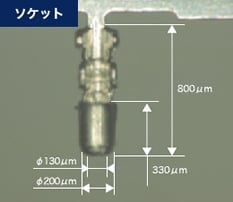
加工材料
黄銅(板厚50μm)
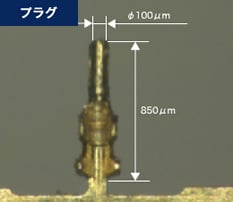
表面処理
Niめっき
資料ダウンロード
株式会社鈴木の特長やプレス加工技術を紹介した資料をダウンロードできます。